1. materials commonly used in sheet metal process
Cold rolled steel
Cold-rolled products are mainly used in construction, light industry, home appliances, electromechanical, automobile and other industries. The product has the characteristics of high accuracy of shape and geometric dimensions, stable performance of the same roll, and good surface quality.
SGCC
Extremely wide range of small household appliances, where the appearance is good. Spangle points: normal regular spangle and minimized spangle and it is possible to distinguish by its coating: for example, Z12 means the total amount of double-sided coating is 120g/mm2.
SGCC also has a reduction annealing process during hot-dip galvanizing, and the hardness is slightly harder, so the stamping performance of sheet metal is not as good as that of SECC. The zinc layer of SGCC is thicker than that of SGCC, but it is easier to process when the zinc layer is thicker. Zinc is removed, and SECC is more suitable for complex stamping parts.
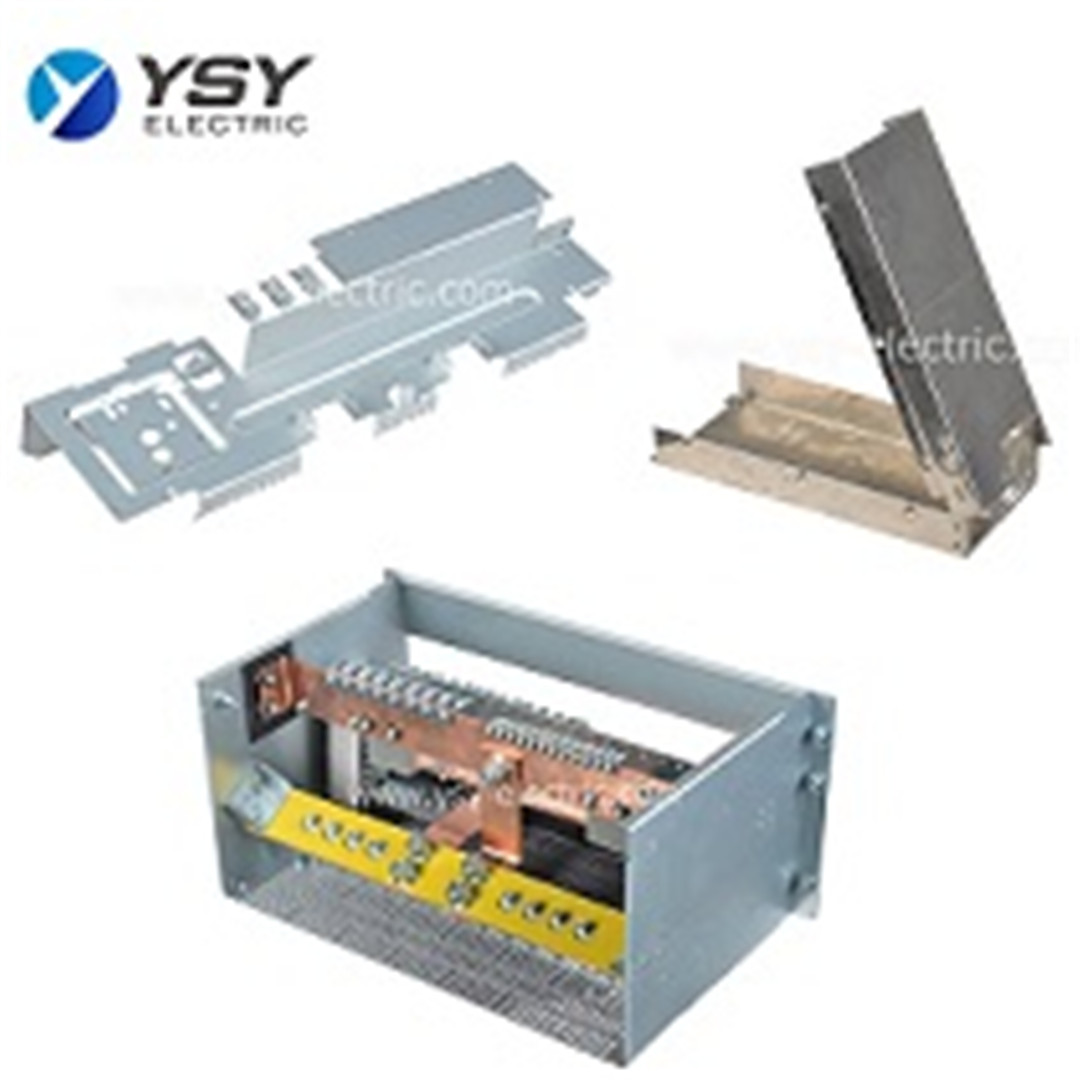
5052 Aluminum alloy
5052 aluminum alloy has some of the best welding characteristics, has great finishing qualities, has excellent saltwater corrosion resistance, but is not easily machined. This alloy is also not heat-treatable and can only be strengthened using the work-hardening process, with 5052-H32 being the most common procedure (for more information on work-hardening, feel free to visit our article all about 5052 aluminum alloy. Type 5052 aluminum is also considered the strongest of the non-heat treatable alloys. For these reasons, 5052 aluminum works exceptionally well as sheet and plate metal, combining excellent formability and weldability with increased strength. Al. 5052 aluminum does not contain any copper, which means it is not as susceptible to salt water corrosion as other aluminum alloys, making it a perfect choice for marine applications. It also is often used in electronic enclosures, hardware signs, pressure vessels, and medical equipment.
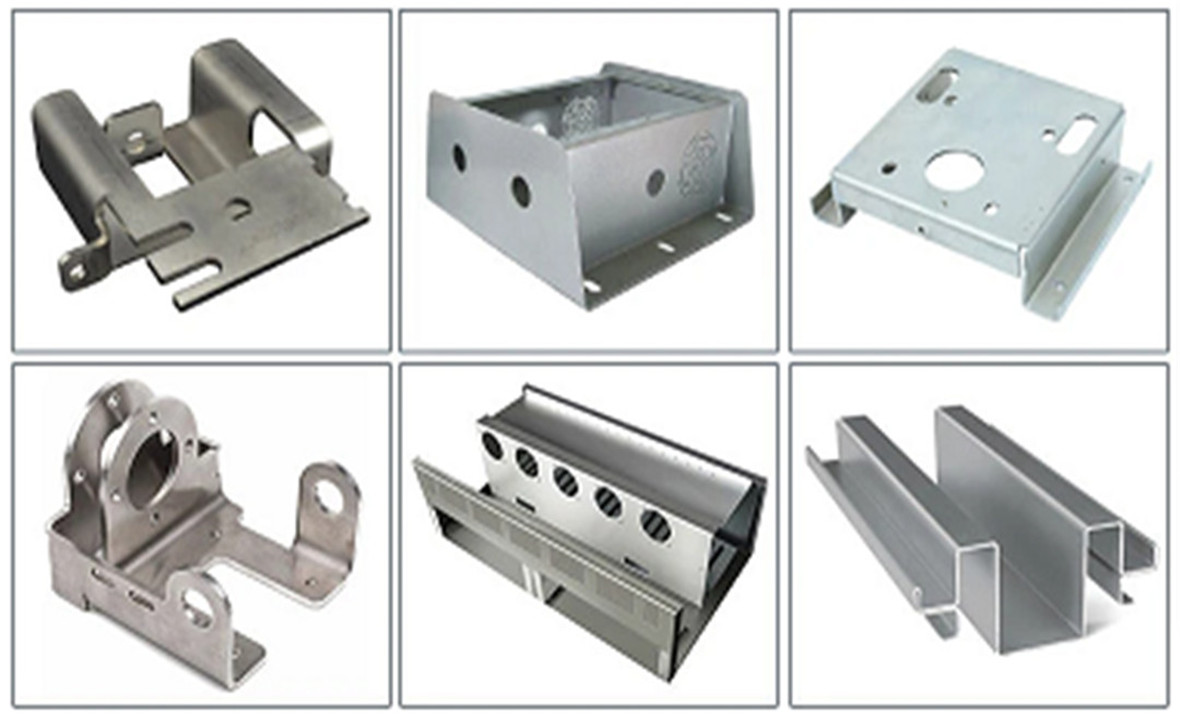
Stainless Steel 304
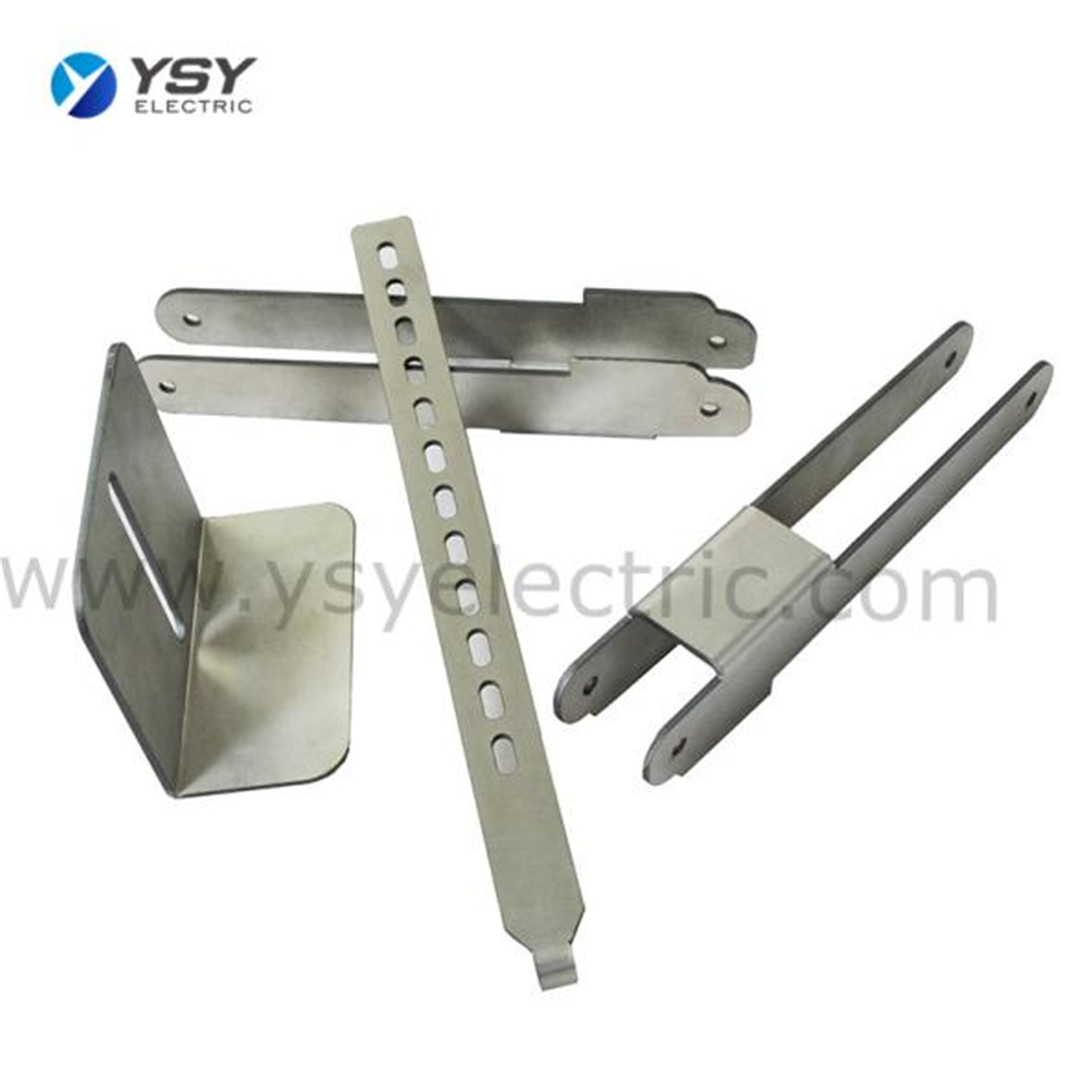
SUS 304 is a general purpose stainless steel that is widely used to make equipment and parts that require a good combination of properties (corrosion resistance and formability).
Stainless Steel 316
SUS316 used to manufacture Blades, mechanical parts, petroleum refining devices, bolts, nuts, pump rods, Class 1 tableware (cutlery and fork)
2. Common surface treatments for sheet metal
Electroplate:
The technology of depositing well-adhered metal coatings with different performance matrix materials on mechanical products by electrolysis. The electroplating layer is more uniform than the hot-dip layer, and is generally thinner, ranging from several microns to tens of microns. By electroplating, decorative protective and various functional surface layers can be obtained on mechanical products, and workpieces that are worn and machined incorrectly can also be repaired. In addition, there are different functions according to various electroplating needs. An example is as follows:
1. Copper plating: used as a primer to improve the adhesion and corrosion resistance of the electroplating layer.
2. Nickel plating: used as a primer or as an appearance to improve corrosion resistance and wear resistance (among them, chemical nickel is more wear-resistant than chrome plating in modern technology).
3. Gold plating: Improve conductive contact resistance and improve signal transmission.
4. Palladium-nickel plating: Improves conductive contact resistance, improves signal transmission, and has higher wear resistance than gold.
5. Tin and lead plating: improve the welding ability, and will soon be replaced by other substitutes (because most of the lead is now plated with bright tin and matte tin).
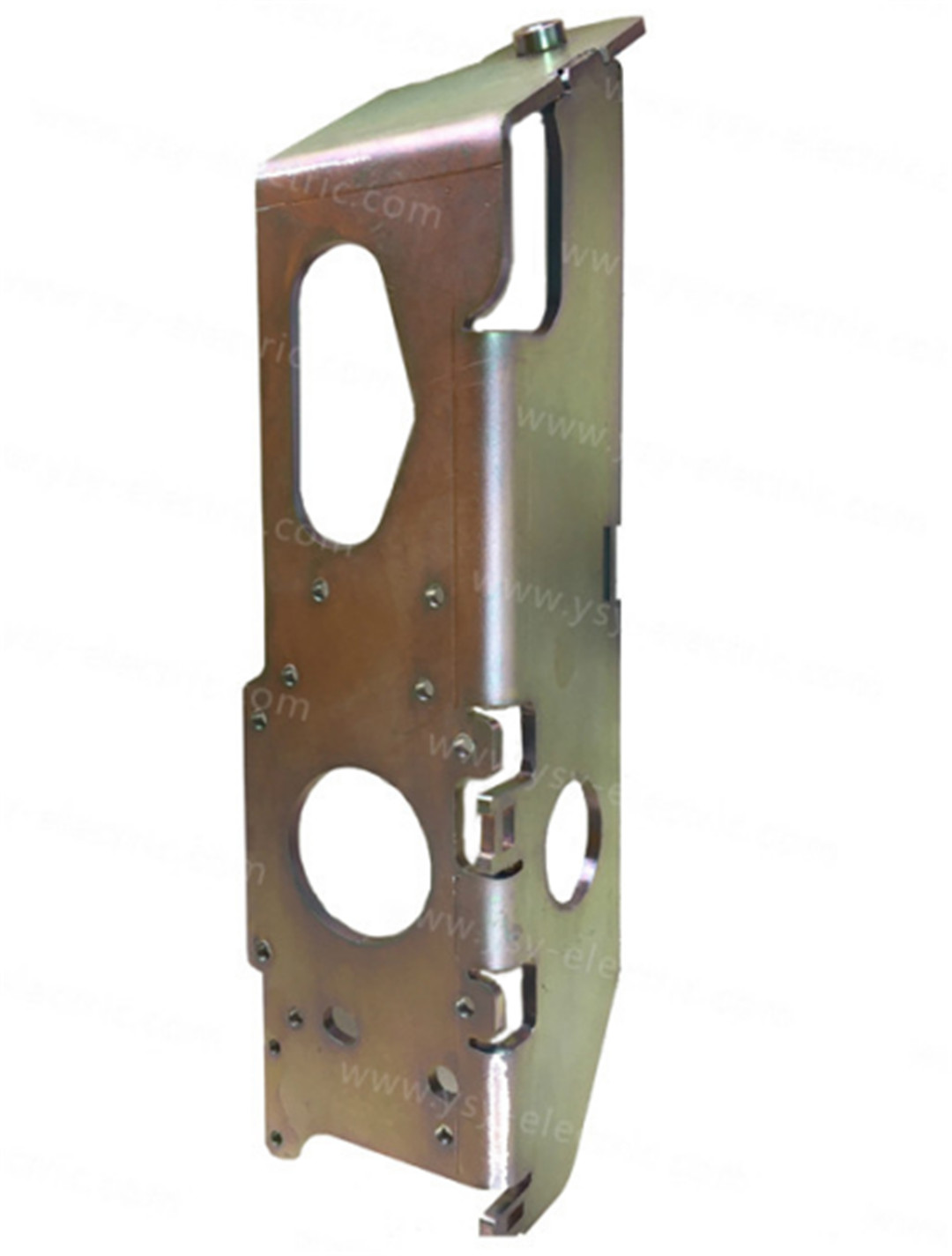
Powder Coating/Coated:
1. A thicker coating can be obtained by one coating. For example, a coating of 100-300 μm needs to be coated 4 to 6 times with a common solvent coating, while this thickness can be achieved with a powder coating at one time. . The corrosion resistance of the coating is very good. (We recommend that you pay attention to the "Mechanical Engineer" public account, and master the knowledge of dry goods and industry information as soon as possible)
2. The powder coating contains no solvent and no pollution of the three wastes, which improves the labor and hygiene conditions.
3. New technology such as powder electrostatic spraying is adopted, which has high efficiency and is suitable for automatic assembly line painting; the powder utilization rate is high and can be recycled.
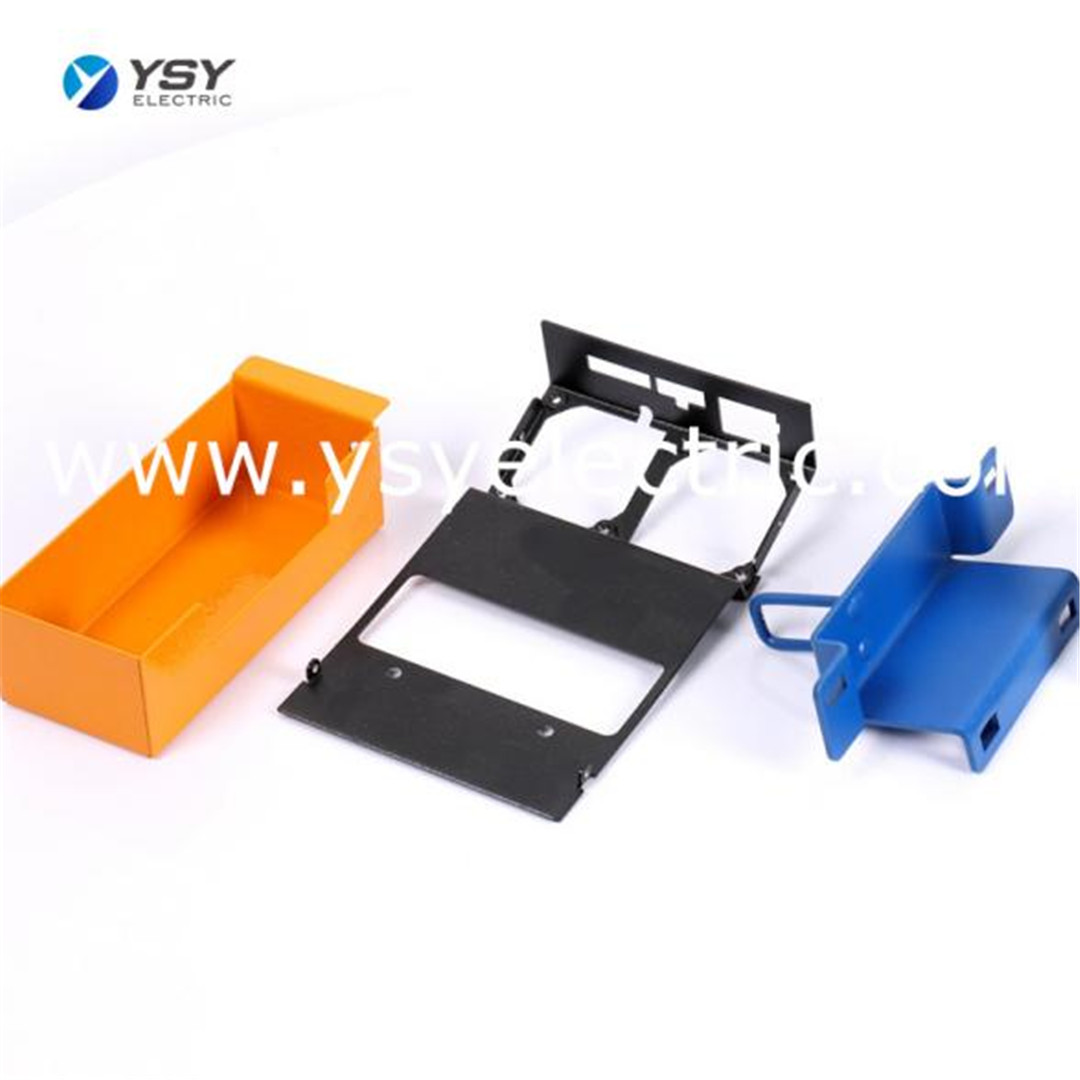
4. In addition to thermosetting epoxy, polyester, acrylic, there are a large number of thermoplastic grease-resistant can be used as powder coatings, such as polyethylene, polypropylene, polystyrene, fluorinated polyether, nylon, polycarbonate and various Fluorine resin, etc.
Electrophoresis
Electrophoretic paint film has the advantages of full, uniform, flat and smooth coating. The hardness, adhesion, corrosion resistance, impact performance and penetration performance of electrophoretic paint film are obviously better than other coating processes.
(1) The use of water-soluble paint and water as the dissolving medium saves a lot of organic solvents, greatly reduces air pollution and environmental hazards, is safe and hygienic, and avoids the hidden danger of fire;
(2) The coating efficiency is high, the coating loss is small, and the utilization rate of the coating can reach 90% to 95%;
(3) The thickness of the coating film is uniform, the adhesion is strong, and the coating quality is good. All parts of the workpiece, such as inner layers, depressions, welds, etc., can obtain a uniform and smooth paint film, which solves the problem of other coating methods for complex shape workpieces. coating problems;
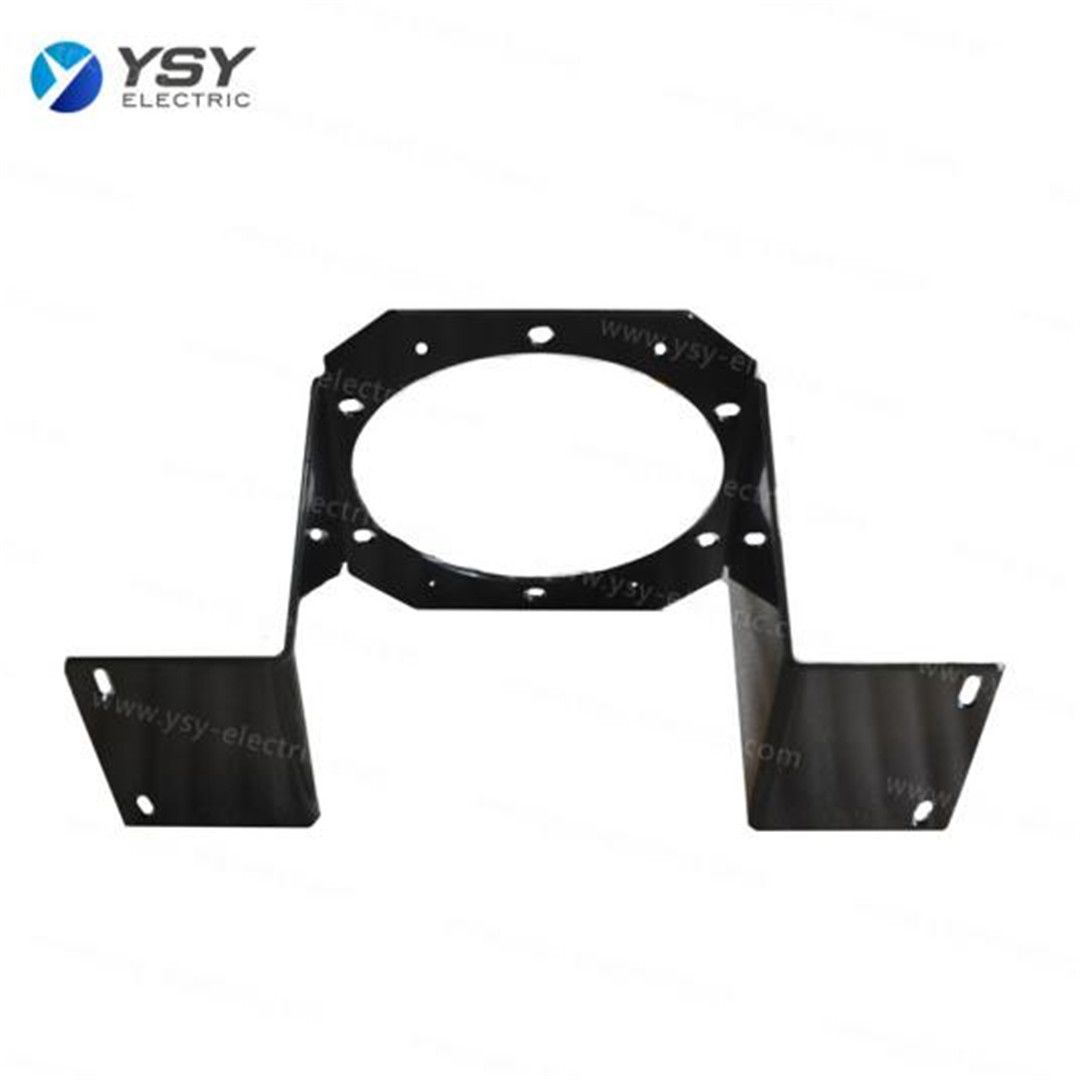
(4) High production efficiency, automatic continuous production can be realized in construction, which greatly improves labor efficiency;
(5) The equipment is complex, the investment cost is high, the power consumption is large, the temperature required for drying and curing is high, the management of paint and coating is complex, the construction conditions are strict, and wastewater treatment is required;
(6)Only water-soluble paint can be used, and the color cannot be changed during the coating process, and the stability of the paint after being stored for a long time is difficult to control. (7) The electrophoretic coating equipment is complex and the technology content is high, which is suitable for the production of fixed color.
Post time: Jun-07-2022